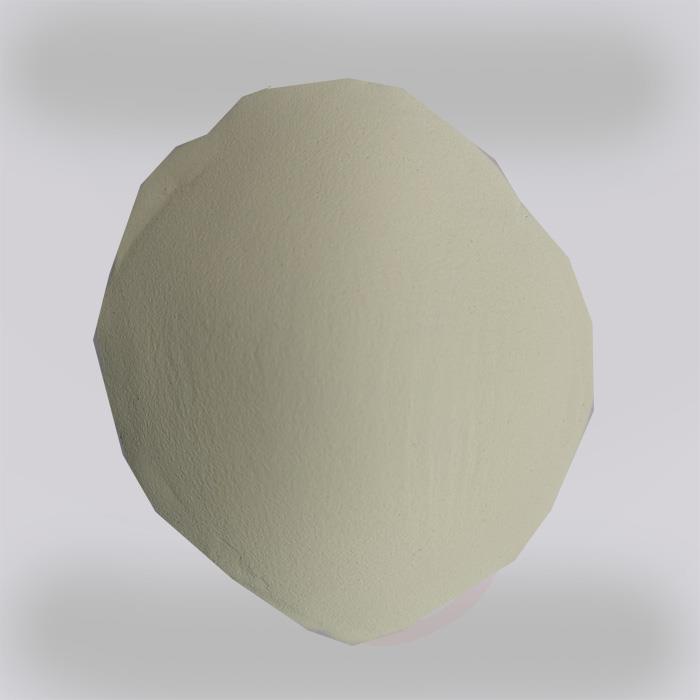
Ceramic sand
Product name: Ceramic sand, special abrasive for sandblasting machine and shot blasting machine
Product model: 30-220#
product advantages
1. The density is between glass sand and steel shot iron sand, and the hardness is greater. In the range of sandblasting strength, it can fill the upper and lower limit blind areas of glass sand and steel shot iron sand.
2. The weight of ceramic sand is light, but the hardness is high, which is very suitable for metal sandblasting strengthening and forming such as titanium alloy, aluminum alloy and high temperature alloy
3. More environmentally friendly, no iron pollution to processed parts; less dust, cleaner working environment, no hidden dangers of silicosis, and harmless to humans.
4. The ceramic sand is not deformed during recycling and has low abrasion, which can ensure the consistency of the surface sandblasting effect during mass production.
5. The ceramic sand has high sphericity, smooth surface and low loss of equipment
6. Ceramic sand has a wider range of particle size, which can meet more application requirements.
Features
1. Ceramic silicon has a spherical shape, a smooth surface, no damage to the workpiece, high hardness, long life, and good elasticity. During the sanding process, the sand grains rebound at multiple angles. The sleeve is often suitable for (metal, plastic) complex workpieces and has the ability to eliminate skin. Improve the fatigue life of the workpiece.
2. Ceramic sand can be used as a blessing ring to reduce the frequency of changing materials and improve production efficiency. The sandblasting process is not easy to be broken, no dust, no metal pollution, clean and environmentally friendly, no hidden dangers of silicosis, which is helpful to the health of employees
3. Compare the effect of glass sand. The degree of photometry is higher, and the life span is increased by about 20-301
4. Compared with steel shot and iron sand, the essence is lower, and there is no iron pollution to the workpiece. No metal powder remains on the surface of the workpiece and no color cast phenomenon to restore the metal color.